To make polypropylene bags, you'll start with granules heated and mixed with additives. Then, the granules are extruded into flat tapes, which are woven into fabric using circular looms. This strong fabric may undergo coating and lamination for added moisture resistance. After that, the fabric is cut to size and sewn, ensuring durability and precise dimensions. Quality control checks are critical throughout this process, ensuring your bags meet safety standards. Interested in the various types of polypropylene bags and their specific applications? You might find the differences intriguing as you continue your exploration.
Key Takeaways
- Polypropylene granules are heated and mixed with additives, then extruded into flat tapes for fabric production.
- Circular weaving machines interlace warp and weft tapes to create durable polypropylene fabric.
- Coating and lamination apply additional layers for moisture resistance, enhancing bag durability.
- The fabric is cut to size and sewn with strong polyester threads for robust seams.
- Finished bags are volumetrically packed using hydraulic machines, ready for shipping.
Overview of the Production Process
The production process of polypropylene bags is a well-orchestrated sequence of steps that transforms raw materials into durable packaging solutions.
It begins with granulation, where polypropylene granules are heated and mixed with additives to enhance performance. These granules are then extruded into flat tapes, which serve as the foundation for the woven fabric.
Next, circular weaving machines take these flat tapes and create tubular fabric, producing around 2300 meters in just 24 hours. This woven fabric is crucial for ensuring the strength and reliability of the bags.
After weaving, the fabric undergoes coating and lamination processes, where additional layers of polypropylene or polyethylene are applied. This step improves moisture resistance and durability, making the bags even more effective for various uses.
Once the fabric is properly coated and treated, it's time for cutting. The woven fabric is cut to the desired size, and then the pieces are sewn together to form the bags.
Finally, the finished bags are baled for efficient shipping. This systematic production process ensures that you receive high-quality polypropylene bags tailored to your needs.
Key Steps in Manufacturing
In the manufacturing of polypropylene bags, several key steps ensure quality and efficiency. It all begins with the drawing of polypropylene tapes, where raw materials are heated and extruded into uniform structures.
Next, the circular weaving process takes over, interlacing warp and weft tapes on circular looms to create polypropylene fabric. You can produce around 2300 meters of fabric in just 24 hours, with varying weaving densities tailored to specific needs.
Following this, the coating and lamination stages apply melted polypropylene and polyethylene to optimize moisture resistance. Attention to resin ratios and temperature settings is crucial for maintaining quality control.
Afterward, the cutting and sewing stage uses advanced machinery to deliver precise dimensions and robust seams, with polyester threads preferred for their superior tensile strength over traditional cotton.
Finally, in the baling process, hydraulic machines pack the finished bags volumetrically, maximizing packing efficiency before shipping.
Each step in the woven bags manufacturing journey is essential, ensuring that the final product meets both durability and functionality for customers worldwide.
Quality Control Measures
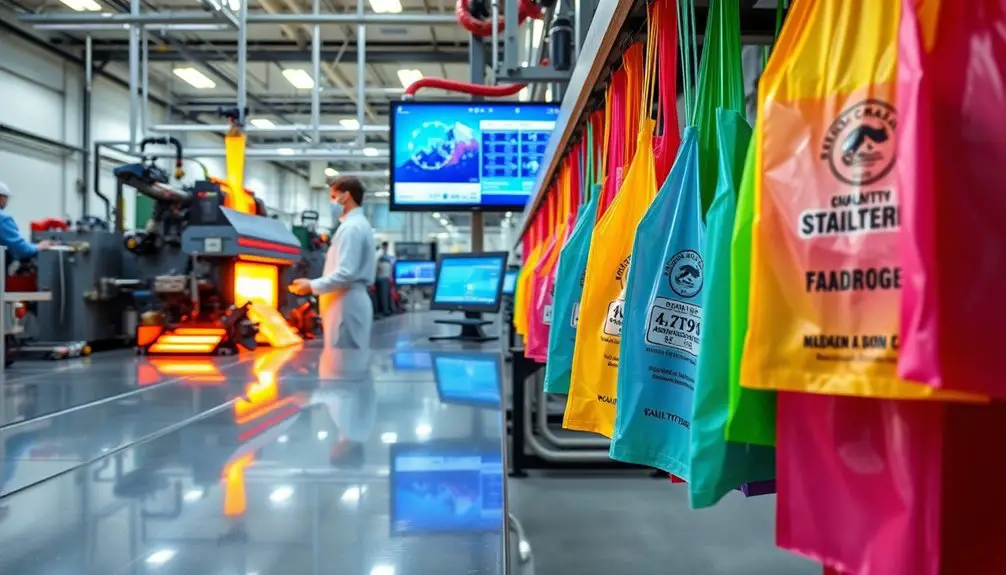
Quality assurance plays a vital role in the manufacturing process of polypropylene bags, ensuring that every product meets high standards. It all starts with strict quality control, where high-quality polypropylene granules are selected and tested to guarantee material integrity. This step is crucial for the durability of the final product.
Next, fabric inspection takes place after weaving. Here, uniformity and adherence to specified weaving standards are checked, along with careful scrutiny for defects that could compromise the bag's quality.
During the cutting and sewing phases, dimensional accuracy is verified, ensuring each bag meets precise measurements essential for functionality and load capacity.
Random samples undergo load testing to confirm their ability to support specified weights without failure, a key factor for safety and reliability for you, the end-user. Throughout the production process, compliance with international safety standards is prioritized.
Rigorous evaluations and documentation help maintain certification and customer trust, assuring you that every polypropylene bag you receive is manufactured with diligence.
Environmental Considerations
Polypropylene bag manufacturers face increasing pressure to address environmental concerns linked to their products. These bags can take decades to degrade, raising significant worries about their long-term ecological impact.
To counter this, many companies are focusing on recycling woven polypropylene bags, which involves cleaning and processing used bags into reusable plastic particles. This approach not only reduces waste but also helps create new products from recycled materials.
With the global market demand for polypropylene bags continuing to rise, there's a pressing need for sustainable practices throughout the production process. Innovative manufacturing techniques are being employed to minimize environmental effects, such as reducing energy consumption and incorporating eco-friendly materials.
Additionally, companies are actively developing biodegradable alternatives that can provide the functionality of traditional polypropylene bags while lessening their ecological footprint. Enhanced recycling programs are also being adopted to ensure that more bags are reused rather than discarded.
As a result, companies are shifting towards advanced recycling methods, which not only reduce waste but also conserve energy by up to 66% in manufacturing processes.
Differences in Bag Types
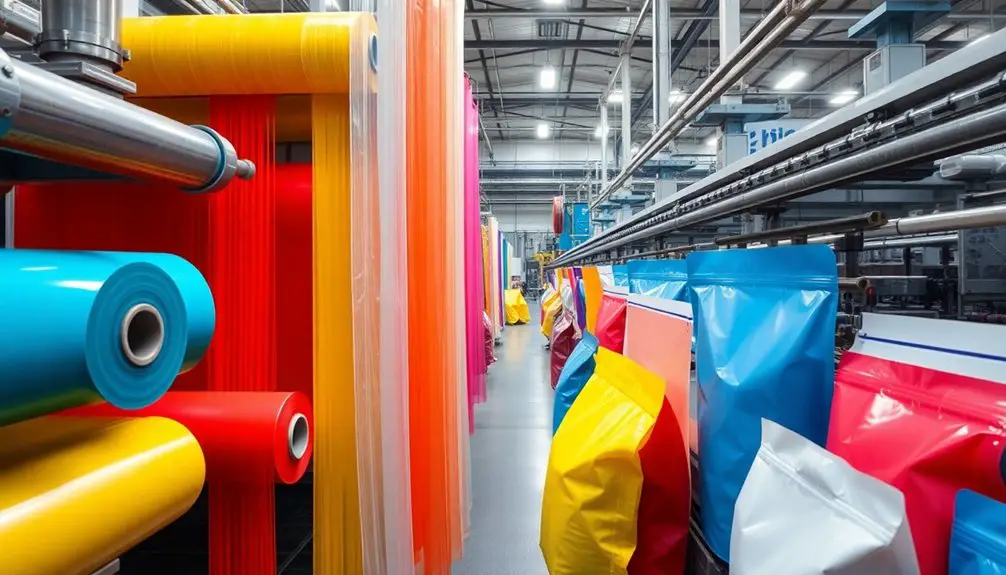
Several types of bags made from polypropylene cater to different needs and applications, each offering unique advantages.
Woven bags, made from interlaced polypropylene tapes, are highly durable and perfect for heavy-duty applications, particularly in agricultural and industrial uses. You'll find them capable of handling significant weights, making them an excellent choice for transporting bulk materials.
On the other hand, non-woven bags are constructed by bonding polypropylene fibers together, resulting in a lighter and more flexible option. These bags are typically used for shopping or promotional purposes, providing a cost-effective solution for everyday use.
BOPP laminated bags feature a layer of Biaxially Oriented Polypropylene film, which allows for vibrant multi-color printing and moisture protection. This makes them ideal for retail packaging, ensuring your products stand out on the shelves.
Kraft paper bags, often made from recycled materials, combine the sturdiness of paper with a laminated layer for enhanced durability, commonly used for groceries or food products.
Lastly, FIBC (Flexible Intermediate Bulk Containers) are large, woven polypropylene bags designed for bulk storage and transport, capable of carrying loads from 500 kg to several tons.
Frequently Asked Questions
How Are Polypropylene Bags Made?
You start with polypropylene granules, extruding them into flat tapes. Then, you weave those tapes into fabric, coat it for durability, and finally cut, sew, and test the bags before shipping them to customers.
How Are Plastic Bags Made Step by Step?
To make plastic bags, you start by melting granules into resin. Then, you extrude this resin into thin sheets, cool them, cut, seal, and print designs before finalizing your bags for use.
How Are Paper Bags Made Step by Step?
To make paper bags, you start with recycled paper pulp, process it into sheets, cut them to size, print designs, fold and glue the edges, add handles if needed, and perform quality checks before packaging.
How Are Plastic Bags Made From Polyethylene?
When you make plastic bags from polyethylene, you melt resin, shape it into film, cool and stretch it, then cut and seal it. Finally, you package the bags for distribution to retailers or manufacturers.