To understand how polypropylene is manufactured, you need to know it starts with the polymerization of propylene monomers derived from petroleum. Manufacturers use methods like Ziegler-Natta and metallocene catalysis, along with gas-phase and liquid-phase polymerization techniques. These methods yield various forms of polypropylene, including homopolymers and copolymers. The process involves specific temperatures and pressures to achieve desired properties such as strength and flexibility. Polypropylene is popular in sectors like packaging and automotive due to its durability. If you keep exploring, you'll uncover more about its applications and the environmental challenges it poses.
Key Takeaways
- Polypropylene is manufactured through polymerization of propylene monomers, primarily using Ziegler-Natta and metallocene catalysis methods.
- Gas-phase polymerization operates at 70°C-100°C and 1-20 atm, producing fine polypropylene powder.
- Liquid-phase polymerization techniques include slurry and bulk methods, functioning at 60-80°C under high pressure.
- Different types of polypropylene are produced, including homopolymers, random copolymers, and block copolymers.
- Advanced technologies such as Novolen®, Unipol®, Borstar®, and Spheripol® enhance production efficiency and material properties.
Overview of Polypropylene
Polypropylene (PP) is a versatile thermoplastic polymer that's become a staple in modern manufacturing since its introduction in 1957. This polymer is made through the polymerization of propylene monomers, which are derived from petroleum.
The resulting material is incredibly popular due to its advantageous properties, including high chemical resistance, low moisture absorption, and a melting point of about 160°C. These features make polypropylene suitable for various heat-resistant applications, from automotive parts to packaging.
The manufacturing process of polypropylene primarily utilizes two methods: Ziegler-Natta and metallocene catalysis. Each of these processes plays a crucial role in determining the quality and characteristics of the final product. For instance, Ziegler-Natta catalysts can lead to different polymer structures, which in turn affect the material's strength and flexibility.
Additionally, polypropylene is classified under recycling code #5, indicating that it's recyclable, although its recycling rate lags behind other plastics. Plastic Recycling Rates are a crucial metric in evaluating the sustainability of polypropylene production and use.
Understanding these aspects of polypropylene helps you appreciate its significance in the modern manufacturing landscape and encourages responsible usage and disposal practices.
Key Manufacturing Processes
Utilizing advanced polymerization techniques, manufacturers produce polypropylene through two primary methods: Ziegler-Natta and metallocene catalysis. These processes influence the polymerization of propylene, determining the final product's molecular structure and properties.
In gas-phase polymerization, temperatures range from 70°C to 100°C with pressures of 1-20 atm. This method yields fine polypropylene powder that's ideal for various applications. Notable technologies like Novolen® and Unipol® enhance the efficiency and quality of the gas-phase process.
Alternatively, liquid-phase polymerization techniques, such as slurry and bulk methods, rely on propylene as a solvent, operating at 60-80°C and high pressures. These methods allow for the production of specific polypropylene grades, tailored to meet diverse needs. Technologies like Borstar® and Spheripol® play a critical role in liquid-phase polymerization, providing unique benefits.
The polymerization process results in different types of polypropylene, including homopolymers, random copolymers, and block copolymers. Each type is designed for specific industrial and consumer applications, ensuring the versatility of polypropylene products in the market.
Properties of Polypropylene
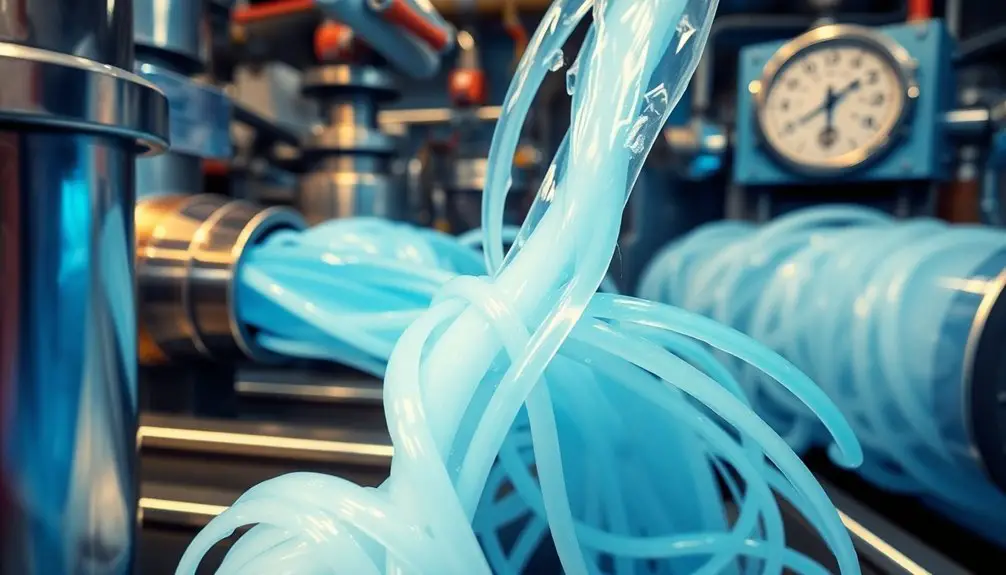
When it comes to versatile materials, polypropylene (PP) stands out due to its impressive properties. One of its most notable features is its high melting point, around 160°C, which makes it suitable for applications requiring heat resistance.
In addition, polypropylene exhibits excellent fatigue resistance, allowing it to endure repeated bending without breaking. This quality is particularly beneficial for living hinge designs.
The density of polypropylene ranges from 0.895 to 0.93 g/cm³, making it the lowest density commodity plastic, perfect for lightweight applications. Its good electrical insulation properties further enhance its appeal, making it a preferred choice for various electronic components.
Moreover, the mechanical properties of polypropylene, such as Young's modulus, fall between 1300 and 1800 N/mm². This range indicates a balance of toughness and flexibility, which is essential for many manufacturing processes.
Applications and Uses
A significant portion of polypropylene's applications can be seen across various industries, showcasing its versatility and practicality.
In packaging, it accounts for about 30% of the global market, especially in containers, films, and closures for food products. Its excellent moisture barrier properties make it a top choice. However, with growing concerns about environmental impact and health risks associated with certain types of plastics, alternatives such as Glass Containers are being explored for food storage.
In the automotive sector, you'll find polypropylene in components like bumpers and dashboards, where its lightweight nature and high impact resistance contribute to improved fuel efficiency.
The medical field also benefits from polypropylene, using it for syringes, surgical instruments, and sterile packaging. Its chemical resistance and ability to withstand steam sterilization are crucial for safety and hygiene.
In textiles, polypropylene is used in carpets, upholstery, and nonwoven fabrics, offering durability and moisture resistance for both residential and industrial applications.
Moreover, polypropylene injection molding is commonly utilized to produce a variety of consumer products, including storage bins, kitchenware, and toys. This method allows for intricate designs and efficient production, making it a go-to for many household items.
Environmental Considerations
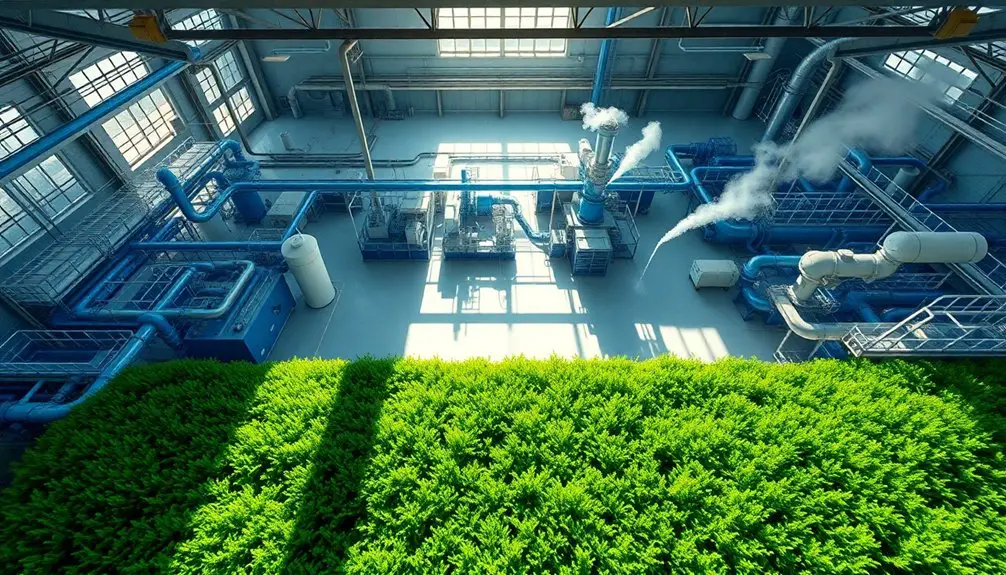
Many people may not realize that polypropylene, despite being a widely used plastic, has significant environmental considerations. While polypropylene has a high production efficiency and generates lower carbon emissions compared to other plastics, its lifecycle still poses challenges.
Notably, the recycling processes for polypropylene aren't as advanced as those for more commonly recycled plastics like PET, leading to a lower recycling rate. However, initiatives are in place to improve this infrastructure.
Another concern is polypropylene's sensitivity to UV degradation. When products made from this material are discarded, they can contribute to environmental issues unless treated with UV stabilizers during production.
Although these additives help extend the material's lifespan, they must be managed carefully to minimize their environmental impact.
Research is also ongoing into biodegradable alternatives to polypropylene, aiming to reduce the long-term effects of plastic waste.
As you consider the benefits and drawbacks of polypropylene, it's essential to weigh its lower emissions and recycling potential against these environmental concerns. By staying informed, you can make better decisions regarding the use and disposal of polypropylene products.
Moreover, it is worth noting that polypropylene's environmental footprint is further exacerbated by the impact of single-use plastics, such as plastic utensils, which contribute significantly to global plastic pollution and harm marine life.
Frequently Asked Questions
How Is Polypropylene Manufactured?
You manufacture polypropylene by polymerizing propylene gas using catalysts like Ziegler-Natta or metallocene. This process occurs under controlled temperatures and pressures, resulting in fine powder or pellets tailored for various applications through additives and modifications.
What Are the Raw Materials for Polypropylene?
To make polypropylene, you need propylene, a gaseous hydrocarbon derived from fossil fuels. You'll also use catalysts like Ziegler-Natta or metallocene and various additives to enhance the properties of the final product.
Who Is the Largest Manufacturer of Polypropylene?
You'll find that LyondellBasell Industries is the largest manufacturer of polypropylene, boasting an impressive annual production capacity of about 6.4 million metric tons. Other significant players include ExxonMobil and SABIC, but LyondellBasell leads the market.
How Is Polypropylene Sourced?
You'll find polypropylene is primarily sourced from propylene, a byproduct of petroleum refining and natural gas processing. Major producers extract it in large petrochemical complexes, relying heavily on fossil fuels for production.