Epoxy can struggle to stick to many plastics, especially low-energy ones like polyethylene and polypropylene. However, with proper surface preparation, you can achieve a solid bond. Start by cleaning the surfaces to remove any contaminants, then sand them to create a mechanical key. Choose an appropriate epoxy, such as a specialty one designed for plastics like PVC, for better results. Always follow mixing instructions and apply evenly. Clamping during curing helps maintain alignment and strengthens the bond. If you want to discover more about tackling specific bonding challenges, keep exploring techniques and materials to enhance your results.
Key Takeaways
- Epoxy generally bonds well with thermosets but struggles with low surface energy thermoplastics like polyethylene and polypropylene.
- Surface preparation, including cleaning and sanding, significantly enhances epoxy adhesion to plastics.
- Specialty epoxies and surface treatments can improve bonding with difficult plastics like PVC and HDPE.
- Fast cure epoxies are available for quick repairs, but curing times vary with temperature and humidity.
- Always follow manufacturer's instructions for mixing and application to ensure effective bonding.
Understanding Epoxy and Plastic
Understanding epoxy and plastic is crucial for successful bonding in various applications. When you're working with epoxy, it's important to recognize that it's a thermoset, meaning it doesn't bond well with many thermoplastics like polyethylene, polypropylene, and polyvinyl chloride.
However, epoxy excels when bonding with thermosets such as polyester or vinylester. If you're considering PVC, specialty epoxies can bond effectively, but you'll need to treat the surface first. Surface treatment methods like plasma or flame treatment can enhance compatibility and improve bond strength by modifying the plastic's surface chemistry.
Keep in mind that the bond strength varies significantly based on the type of plastic and how well you prepare the surface. Accurate mixing of the resin and hardener is key; any inconsistency can weaken the bond. Additionally, remember that low molecular weight epoxy resins are more reactive and can offer better adhesion when used appropriately. Curing temperature also plays a role—heating the epoxy can enhance its performance. Lastly, the microscopic texture of the surfaces can improve mechanical interlocking, further strengthening the bond. The use of proper adhesives is essential for achieving a strong and durable bond between epoxy and plastic surfaces.
Preparing Surfaces for Bonding
Proper surface preparation is key to achieving strong bonds when working with epoxy and plastic. To ensure optimal adhesion, follow these steps: first, clean the surfaces thoroughly to remove any contaminants like grease or dirt. Use solvents such as lacquer thinner or acetone, and make sure to wipe the surface before the solvent dries. Next, ensure that all bonding surfaces are dry; you can speed up this process with a hot air gun or fans. Finally, sand the surfaces using 80-grit aluminum oxide paper to create a mechanical 'key' for the epoxy. Surface cleaning is essential because contaminants can significantly reduce the effectiveness of the bond. Effective epoxy application also requires understanding the Epoxy Cure process to guarantee a strong and durable bond between the epoxy and plastic materials.
Here's a quick reference table summarizing the preparation steps:
Step | Action Required | Purpose |
---|---|---|
Clean | Remove contaminants with solvents | To ensure better adhesion |
Dry | Ensure surfaces are completely dry | To improve epoxy bond strength |
Sand | Abrade with 80-grit sandpaper | To create a mechanical 'key' for bonding |
Inspect | Check for dust or residues after sanding | To maintain a clean surface for adhesion |
Following these steps will significantly increase the chances of a successful bond between epoxy and plastic.
Choosing the Right Epoxy
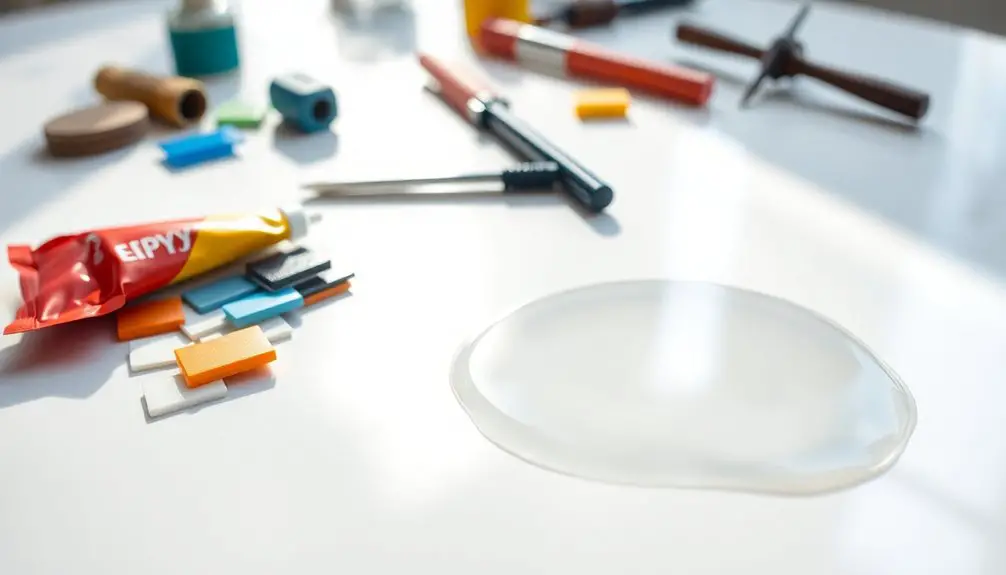
When selecting the right epoxy for your project, it's crucial to consider the specific materials you'll be bonding. Epoxy adhesives come in various formulas, each tailored for different surfaces. The choice of epoxy is also influenced by the need for chemical resistance, which is a key property of materials like polypropylene used in car bumpers.
For general bonding, a versatile general-purpose epoxy works well on plastics like ABS, PVC, and acrylic. If you're working with ABS, consider a specialty epoxy like Loctite Plastic Bonder, which offers high impact and water resistance. Additionally, be aware that specific adhesives are needed for some plastics like PVC and HDPE, which can be difficult to glue.
For PVC, a specialty epoxy or surface treatment may enhance bonding strength. Acrylic typically requires an acrylic solvent adhesive for optimal adhesion, while polycarbonate is best bonded with epoxy, though surface modification is necessary for a secure bond.
Fast cure epoxies, such as Lightning Tumblers Epoxy Resin, are excellent for quick repairs as they cure in under an hour. Remember that temperature affects curing time; warmer conditions speed up the process.
Before applying epoxy, ensure surfaces are clean, dry, and properly prepped. Roughening smooth surfaces can significantly improve adhesion.
Effective Application Techniques
For successful bonding with epoxy, effective application techniques are essential. Start by thoroughly cleaning the plastic surface to remove any contaminants or oils that could hinder adhesion. It is also crucial to consider the plastic types and their unique bonding properties to ensure a strong and durable bond.
Next, roughen the surface using sandpaper to enhance mechanical interlocking. If you're working with thermoplastics, consider flame oxidation to improve chemical adhesion.
When mixing your epoxy, follow the manufacturer's instructions closely to achieve a uniform mixture of resin and hardener. Apply the mixed epoxy evenly to both surfaces, ensuring you avoid excess. Use clamps to hold the pieces together during the curing process, maintaining proper alignment and pressure. Remember to allow the epoxy to cure for the recommended time, typically between one to three hours.
While clamping, ensure the parts fit together properly and use clamps that apply even pressure. Avoid over-clamping, which can create uneven bonding or squeeze out the epoxy.
Finally, monitor the curing process for any bubbles or defects. Once fully cured, inspect the bonded area for any weaknesses and conduct tests to ensure the bond's durability before exposing it to stress or environmental factors. Additionally, ensure you choose the right epoxy formula for the specific type of plastic you are working with to achieve optimal results.
Overcoming Bonding Challenges
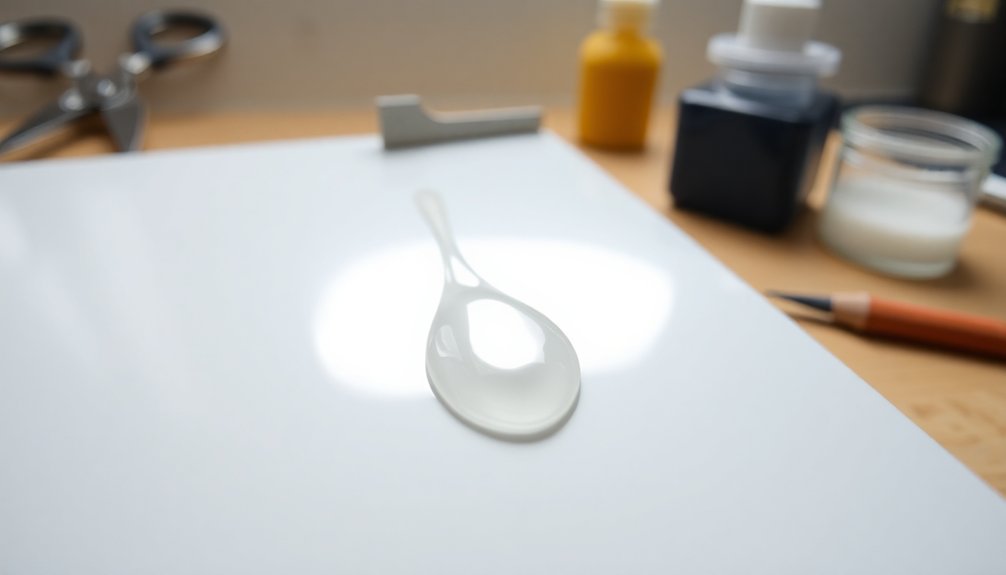
Bonding challenges can arise at any stage of your project, but recognizing and addressing them early can lead to successful outcomes.
Start with proper surface preparation; sand the plastic with 80-grit sandpaper to create keying grooves for better adhesion. Consider flame treating the surface to oxidize it, enhancing the bond strength. Always clean the surface with denatured alcohol to remove contaminants that could inhibit bonding. Keep in mind that some plastics, such as polyolefins (PE, PP), exhibit low surface energy, which can make bonding more challenging. Effective plastic welding techniques can also be used to join plastics, offering a strong and durable bond.
Choosing the right adhesive is crucial. Use epoxies specifically designed for plastics, like G-flex epoxy, or cyanoacrylate with a primer like Permabond POP for better adhesion, especially on polyolefins.
Be mindful of substrate issues; ensure the bonding area is clean and large enough to provide strength. Avoid excessive pressure during clamping, as it can squeeze epoxy out of the joint.
Finally, account for environmental factors. Adjust for temperature by allowing extra curing time in cooler conditions, and check the resin-to-hardener ratio to ensure complete curing. Avoid high humidity when bonding, and store adhesives in controlled conditions to maintain their effectiveness.
Frequently Asked Questions
Can Epoxy Bond Two Different Types of Plastics Together?
Yes, you can bond two different types of plastics with epoxy, but success depends on the specific plastics involved. Proper surface preparation, like sanding or treating, enhances the bond strength significantly for better results.
What Is the Maximum Temperature Epoxy Can Withstand After Curing?
After curing, most epoxies can withstand temperatures between 40°C and 130°C. Some high-temperature-resistant varieties can handle up to 145°C, but watch out—exceeding 200-250°C can cause them to lose their structure.
How Can I Remove Excess Epoxy From Plastic Surfaces?
To remove excess epoxy from plastic surfaces, soak a paper towel in isopropyl alcohol and gently rub it on the area. For cured epoxy, apply acetone or heat to soften before scraping it away.
Is There a Specific Epoxy for Flexible Plastic Materials?
Yes, there're specific epoxies designed for flexible plastics, like MT382 and AA-BOND 2170. They offer excellent bonding, flexibility, and low viscosity, making them perfect for various applications, including automotive and electronics.
How Long Does Epoxy Take to Cure in Cold Temperatures?
In cold temperatures, epoxy can take 24 to 72 hours to cure, with potential delays below 50°F. To ensure proper bonding, maintain a stable, warmer environment and monitor the curing process closely.