Yes, ABS plastic is considered food safe by the FDA and EFSA. It's commonly used in food processing equipment and packaging due to its excellent heat and chemical resistance. However, you should be cautious since certain additives and potential chemical leaching can pose health risks, particularly with acidic or fatty foods. It's essential to choose BPA-free ABS to minimize endocrine disruption concerns. While ABS is generally reliable, understanding specific applications and handling practices can further ensure safety. If you're interested in the nuances of ABS plastic's safety and its applications, you'll find more insights ahead.
Key Takeaways
- ABS plastic is deemed safe for food contact by both the FDA and EFSA, provided it meets regulatory standards.
- It exhibits excellent heat and chemical resistance, making it suitable for food processing applications.
- BPA-free ABS is recommended to mitigate health risks associated with endocrine disruptors and chemical leaching.
- Prolonged exposure to moisture and temperature extremes may cause stress cracking in ABS, affecting its safety for food contact.
- Caution is advised when using ABS with acidic or fatty foods to reduce the risk of leaching harmful substances.
General Safety Considerations
When considering the safety of ABS plastic for food use, it's vital to understand its regulatory compliance and formulation. ABS plastic is generally deemed safe for food contact by agencies like the FDA and EFSA, ensuring that it meets strict safety standards. In the EU, manufacturers must limit acrylonitrile monomer residue to below 10 parts per million, providing an added layer of safety. You'll find BPA-free ABS options available, which are designed to reduce health concerns linked with endocrine disruptors. Additionally, ABS is safe for food processing when used properly, highlighting its versatility in various applications. The safety of ABS plastic is also dependent on the type of plastic resin used, such as those with recycling codes, which can impact the potential for chemical leaching. To ensure safety, always select ABS materials specifically formulated and tested for food use. It's crucial to follow the manufacturer's instructions for safe handling and usage. Keep in mind that while ABS has regulatory approval, improper usage can lead to potential issues, like chemical migration, especially under high temperatures or with acidic foods.
Chemical and Physical Properties
Understanding the chemical and physical properties of ABS plastic is vital for assessing its suitability for food applications. ABS is resistant to many aqueous acids and alkalis, making it a robust choice in various environments. However, it's important to note that it can swell when exposed to glacial acetic acid and is attacked by concentrated sulfuric and nitric acids. Additionally, ABS is soluble in esters and ketones, so you'll want to avoid these substances to maintain its integrity. On the thermal side, ABS has a glass transition temperature of about 105 °C (221 °F) and doesn't have a true melting point due to its amorphous nature. Its density ranges from 0.9 to 1.53 g/cm³, and it boasts a high tensile strength, which contributes to its durability. ABS is known for its excellent chemical resistance, allowing it to maintain structural integrity at varying temperatures. With a flammability rating of 1.00, it's relatively safe in terms of fire risk. Finally, ABS exhibits stable electrical properties, making it suitable for various applications beyond food. Knowing these characteristics helps you gauge whether ABS is the right choice for your specific needs, especially in food-related environments. The safety of ABS plastic for food use also depends on the plastic recycling process, which can affect the material's quality and contamination risk.
Applications in Food Industry
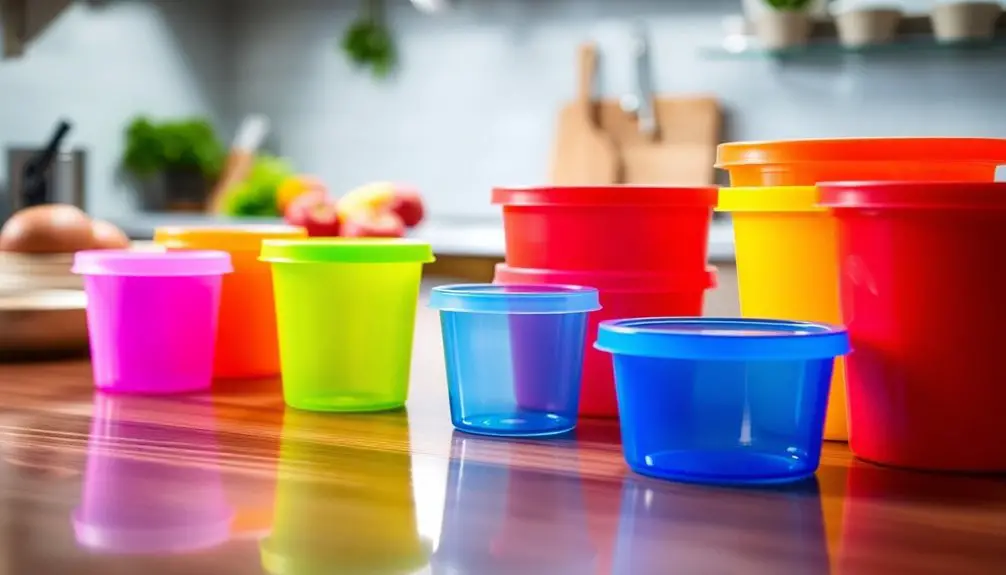
ABS plastic finds a wide array of applications in the food industry, making it a versatile material for various purposes. Its unique properties allow it to be safely used in different food-related applications, ensuring both functionality and compliance with safety standards. The use of ABS plastic in the food industry also raises concerns about chemical leaching and the potential impact on human health and the environment.
Here are some key applications of ABS in the food industry:
- Food Processing Components: ABS is ideal for food processors and refrigerator linings due to its durability and low-temperature resistance.
- Packaging Materials: You can find ABS in attractive and impact-resistant packaging, keeping food fresh and secure.
- Food Handling Components: Its high impact resistance makes ABS suitable for various food handling operations, ensuring safety during use. Additionally, it is classified as non-toxic thermoplastic, which further supports its safe use in food-related applications.
- Industry-Specific Applications: ABS is used in food transport and equipment, thanks to its insulating properties and dimensional stability.
With FDA and EFSA approvals, ABS is recognized for its non-toxic properties and temperature resistance, making it a reliable choice for food contact materials.
Whether you're involved in food processing or packaging, ABS offers a combination of safety, durability, and versatility that's hard to beat.
Potential Risks and Limitations
When using ABS plastic in food-related applications, you need to be aware of potential risks, including chemical leaching concerns. The material's weathering resistance issues can also lead to stress cracking over time, which might compromise safety. It's essential to consider these factors to ensure you're making a responsible choice for food safety. Additionally, it's important to note that ABS is FDA-certified for use in kitchen appliances, which underscores its safe application in some food-related contexts. The use of ABS plastic in food-related applications should also take into account the potential for microplastic particles to be released during the boiling process, posing a risk to human health.
Chemical Leaching Concerns
Concerns about chemical leaching from ABS plastic can significantly impact its safety for food contact. While ABS is generally considered safe, there are potential risks you should be aware of:
- BPA Presence: ABS may contain bisphenol A (BPA), an endocrine disruptor that raises health concerns.
- Chemical Resistance: ABS has limited resistance to certain chemicals, including acetone and benzene, which can leach into food.
- Flame Retardants: Toxic chemicals used as flame retardants in ABS can leach and be absorbed through the skin, posing health risks.
- Regulatory Compliance: Although ABS meets regulations like the EU's food contact materials legislation, specific additives can still affect its safety. Additionally, ABS is classified as non-toxic, which can provide some reassurance regarding its use in consumer products.
To minimize risks, consider using BPA-free ABS and ensure that the product complies with safety standards.
Be cautious about the types of food you store in ABS containers, especially if they contain acidic or fatty substances, as these can increase leaching potential.
Staying informed about the material's properties helps you make safer choices for food contact applications.
Weathering Resistance Issues
Weathering resistance is a critical factor to consider when evaluating the longevity and performance of ABS plastic in various applications. While ABS plastic is versatile, its exposure to environmental elements can lead to significant degradation. Here are some potential risks and limitations you should be aware of:
Issue | Description |
---|---|
UV Degradation | Prolonged sunlight exposure can cause color changes, reduced gloss, and lower impact strength. |
Temperature Extremes | Extreme heat can soften ABS, while sudden temperature changes may lead to cracking. |
Moisture and Humidity | Although hydrophobic, prolonged moisture exposure can cause swelling and eventual degradation. |
Atmospheric Pollution | Airborne pollutants can stain and dull the surface, impacting the aesthetic and durability. |
Understanding these weathering resistance issues is essential for ensuring that ABS plastic performs well in outdoor or variable environments. Stabilizers and antioxidants are often incorporated into ABS formulations to enhance its weather resistance. If you're considering ABS for such applications, be mindful of these limitations to avoid potential failures in performance and appearance.
Stress Cracking Potential
While understanding weathering resistance issues is important for the longevity of ABS plastic, the material's susceptibility to stress cracking represents another significant concern.
Stress cracking can compromise the integrity of ABS products, especially in food contact applications. Here are some key factors that contribute to this issue:
- Material Composition: High levels of monomer residues and potential BPA presence can increase stress cracking risks.
- Manufacturing Process: Inadequate cleaning during production and the use of certain additives can lead to inconsistent quality, heightening stress cracking potential. Moreover, CHIMEI's innovative cleaning process has been shown to effectively reduce acrylonitrile monomer residue below 5 ppm, thereby enhancing the overall safety of ABS.
- Environmental Factors: Prolonged exposure to temperature extremes, high humidity, or solvents can weaken ABS, making it more prone to cracking.
- Applications and Usage: The specific use of ABS products, particularly in structural applications or food processing, requires careful consideration to avoid mechanical stress that could lead to cracking.
Manufacturing and Handling
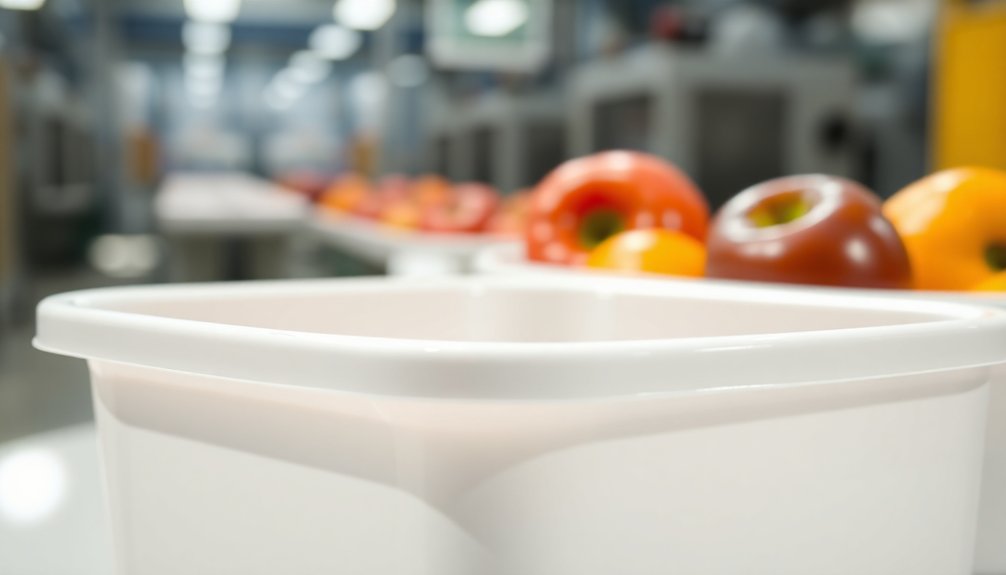
Manufacturing ABS plastic for food contact applications involves a meticulous process designed to ensure safety and quality. The production typically starts with an emulsification process that polymerizes acrylonitrile and polystyrene monomers with butadiene rubber. While some manufacturers may use patented continuous mass polymerization, emulsification remains the standard.
Controlling the levels of acrylonitrile monomer residue is crucial, as compliance with EU standards is necessary for food safety. Advanced cleaning processes further optimize the reduction of monomer residues, which helps maintain high-quality ABS. You'll find that consistent quality control throughout the manufacturing process is vital, as even slight variations in residue can impact safety.
ABS plastic boasts excellent heat and chemical resistance, making it ideal for food processing components. Its durability ensures that it withstands physical stress without deforming, which is important in various applications.
Additionally, ABS is recyclable, aligning with sustainable manufacturing practices. When handling ABS, be aware that the safety of the final product also depends on the specific additives and colorants used during production. Always prioritize materials that meet stringent quality standards for food contact. The production of ABS plastic must also consider the environmental impact, including the use of chemical resistance properties to minimize potential harm.
Regulatory Compliance
Regulatory compliance is vital for ensuring that ABS plastic remains safe for food contact applications. You should be aware that various regulatory agencies, including the FDA and EFSA, have established guidelines that ABS must follow.
Here are some key points to consider:
- FDA and EFSA Guidelines: ABS is generally deemed safe for food contact by these agencies when adhering to their regulations.
- EU Regulations: The EU limits acrylonitrile monomer residue in ABS to below 10 parts per million, ensuring consumer safety.
- Documentation Requirements: Business operators must provide written declarations of compliance, detailing the materials and substances used in production.
- Verification Process: Competent authorities review these declarations for sufficiency and may request further information or testing if necessary.
When handling ABS plastic for food contact, it's also important to consider chemical leaching and the potential health risks associated with certain types of plastics, as outlined by regulatory agencies.
Frequently Asked Questions
Can ABS Plastic Be Used in Microwaves?
Yes, you can use ABS plastic in microwaves if it's labeled microwave-safe and BPA-free. Always check for labels and avoid high heat to prevent melting or warping, ensuring your food stays safe.
Is ABS Plastic Dishwasher Safe?
Yes, ABS plastic is generally dishwasher safe. It withstands mild temperatures and alkaline conditions, with minimal degradation reported. Just ensure you follow manufacturer guidelines to maintain its quality and longevity.
How Long Does ABS Plastic Last in Food Applications?
ABS plastic lasts quite long in food applications, often several years, thanks to its durability, resistance to wear, and ability to withstand temperature extremes. Proper care and maintenance can extend its lifespan even further.
Can ABS Be Recycled After Food Contact?
Yes, you can recycle ABS after food contact, but ensure it's cleaned properly. Chemical residues may affect recyclability, so consider BPA-free options. Following regulatory standards is crucial for maintaining quality and safety during recycling.
What Temperature Can ABS Withstand Safely?
ABS can safely withstand temperatures up to around 85°C (185°F) without losing mechanical properties. Beyond this, it may soften or deform, so avoid exposing it to extreme heat for prolonged periods.