Polypropylene is extracted from propylene gas, which comes from cracking fossil fuels like petroleum and natural gas. This process involves purifying propylene through fractional distillation to achieve high purity levels. After that, it undergoes polymerization using catalysts like Ziegler-Natta at high temperatures and pressures. The final result appears as fine powder or resin pellets. While this common plastic has many uses, its extraction process does have environmental impacts. If you're curious about the innovations aimed at making polypropylene production more sustainable, there's plenty more to uncover.
Key Takeaways
- Polypropylene is extracted from propylene gas, which is derived from cracking fossil fuels like petroleum or natural gas.
- The extraction process includes purifying propylene through fractional distillation to achieve high purity levels.
- Polymerization of purified propylene occurs using catalysts at temperatures of 70°C-100°C and pressures of 1-20 atm.
- The final product appears as fine powder or resin pellets, ready for further processing into various plastic products.
- Innovations in extraction aim to enhance efficiency, reduce waste, and explore renewable energy sources for production.
Overview of Polypropylene
Polypropylene (PP) is a versatile thermoplastic polymer that you often encounter in everyday products. It's produced from the polymerization of propylene gas, which comes from petroleum or natural gas. Since its discovery in the mid-1950s and commercialization in 1957, polypropylene has become the second most manufactured plastic globally, following polyethylene.
One of the standout features of polypropylene is its lightweight nature, making it ideal for various applications. Its high chemical resistance allows it to perform well in environments where other materials might fail. You'll find polypropylene in the packaging industry, where it's used for containers and films, as well as in automotive parts, where durability and weight reduction are crucial.
Additionally, polypropylene exhibits low moisture absorption and can withstand temperatures up to approximately 160°C, further enhancing its usability across different sectors.
While it's categorized under recycling code #5, indicating its recyclability, it does have a lower recycling rate compared to other plastics. Overall, polypropylene's unique properties make it an essential material in modern manufacturing and everyday life.
Extraction Process
The extraction process for polypropylene relies on transforming raw materials derived from petroleum or natural gas into propylene gas through a series of chemical reactions.
First, larger hydrocarbon molecules in fossil fuels undergo cracking, producing propylene gas. After that, the propylene is purified via fractional distillation, ensuring high purity levels.
Next, you'll find that propylene gas undergoes polymerization, typically using catalysts like Ziegler-Natta or metallocene. This process occurs at high temperatures (between 70°C and 100°C) and pressures (ranging from 1 to 20 atm), resulting in long chains of polypropylene molecules.
The final product of this extraction process appears as fine powder or resin pellets, ready for further processing into various plastic products.
Innovations in this field aim to enhance efficiency, reduce waste, and utilize renewable energy sources to minimize the environmental impact associated with polypropylene production.
Manufacturing Techniques
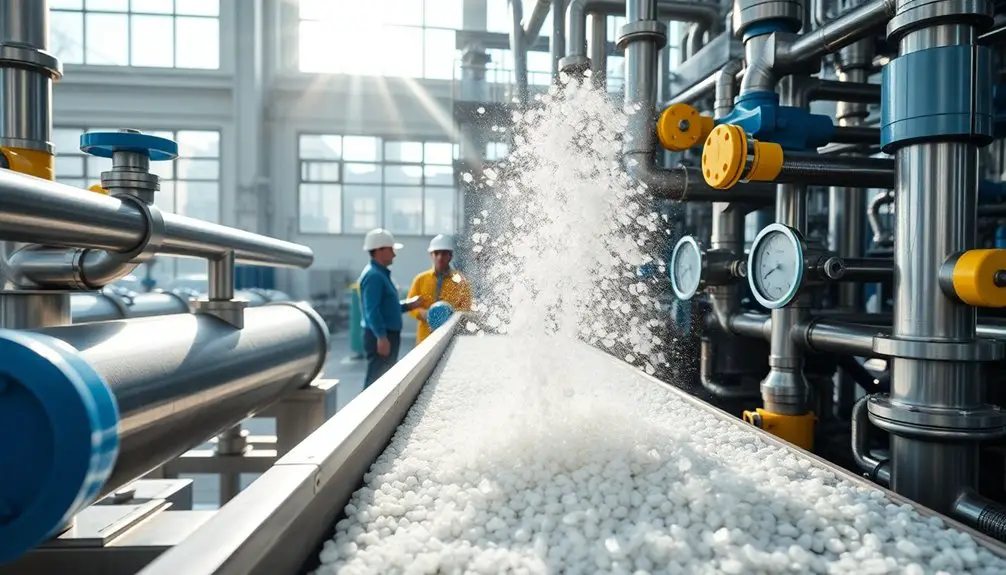
Manufacturing polypropylene involves a variety of techniques that optimize both efficiency and product quality. The primary method for polypropylene production is the polymerization of propylene gas, with two main processes: the Ziegler-Natta process and metallocene catalysis. The Ziegler-Natta process uses titanium-based catalysts, while metallocene catalysts provide precise control over polymer properties, enhancing the final product's quality.
Gas-phase polymerization operates at temperatures between 70°C to 100°C and pressures of 1-20 atm, yielding a fine powder suitable for molding or extrusion. Other techniques include bulk polymerization, which uses liquid propene as a solvent, and slurry polymerization, where C4-C6 alkanes act as diluents while propylene is introduced as gas.
Injection molding is the dominant manufacturing method for polypropylene, allowing for high production rates and complex shapes. The use of advanced processing techniques, particularly metallocene catalysts, results in polypropylene with fewer impurities and improved polymer properties, such as enhanced strength and flexibility. Polypropylene often competes with HDPE plastic for applications requiring high tensile strength and temperature resistance.
Environmental Considerations
With the extraction of polypropylene heavily relying on petroleum and natural gas, environmental concerns have risen significantly. The production process not only contributes to greenhouse gas emissions but also generates harmful waste and byproducts that can lead to air pollution.
Life Cycle Assessments (LCA) estimate that producing just one ton of polypropylene results in approximately 1586 kg of CO₂ emissions, underscoring the urgent need for sustainable practices.
You should consider the ecological damage caused by traditional extraction methods. As companies face increasing pressure to reduce their environmental impact, many are investing in renewable energy sources and closed-loop systems. These initiatives aim to minimize waste and pollution throughout the polypropylene lifecycle, from extraction to production.
To truly address the environmental impact of polypropylene, it's essential to adopt innovative technologies that can lessen greenhouse gas emissions and improve overall sustainability.
As consumers, you're encouraged to support businesses that prioritize eco-friendly practices and transparency about their production processes. By making informed choices, you can contribute to a healthier planet while still benefiting from the versatility of polypropylene in everyday products.
Future Innovations
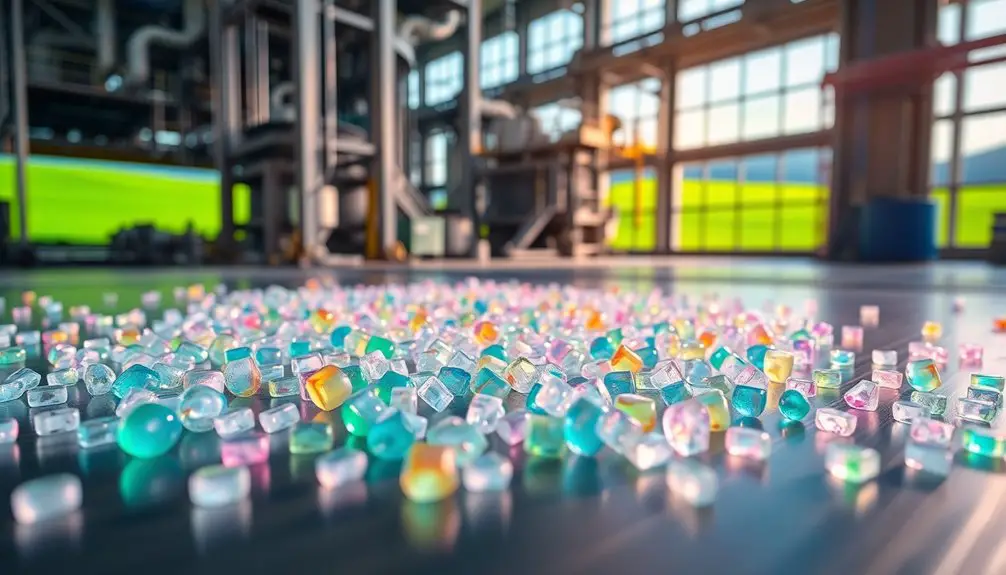
As the demand for more sustainable practices grows, innovations in polypropylene extraction are emerging to address environmental concerns. Future innovations focus on developing metallocene catalysts, which enhance the efficiency of polypropylene production and allow for precise control over the polymer's properties. This technology not only boosts productivity but also reduces the reliance on traditional fossil fuels.
Additionally, research is underway to implement advanced recycling processes, such as water-looping techniques that recycle polymer scraps, minimizing waste and energy consumption during production. Companies are increasingly investing in renewable energy sources to tackle the carbon footprint associated with extraction and production processes.
These steps are vital in reducing greenhouse gas emissions linked to conventional methods. Closed-loop systems are another area of exploration, designed to mitigate ecological damage and promote sustainable practices within the industry.
The continuous investigation into bio-based resources aims to replace fossil fuels, offering a greener alternative for polypropylene production. By embracing these future innovations, you can play a part in fostering a more sustainable approach to plastic manufacturing, ultimately benefiting the environment and society as a whole.
Moreover, utilizing reusable items, such as refillable 100 ml bottles, is crucial in minimizing plastic waste in daily life and has a direct impact on the need for polypropylene extraction.
Frequently Asked Questions
How Is Polypropylene Extracted?
You'll find polypropylene extracted through a chemical process involving petroleum or natural gas. Catalysts and high temperatures convert propylene gas into long polymer chains, forming the plastic that's widely used in various applications today.
What Is the Source of Polypropylene Plastic?
The source of polypropylene plastic is primarily fossil fuels, especially petroleum and natural gas. These materials undergo cracking and polymerization processes, transforming raw hydrocarbons into the versatile polypropylene you see in countless everyday products.
What Is the Source of Polyethylene Plastic?
The source of polyethylene plastic is primarily crude oil and natural gas. You'll find it produced through the polymerization of ethylene gas, which comes from cracking larger hydrocarbons. This process creates various types of polyethylene.
What Resources Are Used to Make Polypropylene?
To make polypropylene, you'll need petroleum or natural gas as primary resources. These materials undergo chemical processing to produce propylene, which then polymerizes into long chains, forming the versatile polypropylene you encounter in various products.